Simplebgc Gui For Mac
The BaseCam SimpleBGC 32-bit controller is used for the construction of high quality 3-axis camera stabilizing systems. This board is deployed in handheld and
This version of the controller (and the new Tiny 32-bit board) is our new direction in the development of the stabilizing solutions. It replaces the previous 8-bit version of the SimpleBGC controller keeping 100% backward compatibility for users replacing an older controller with this one who need all of the functionality of the old controller to be the same in the new controller (in order to fit into the existing system with a minimum of effort). In addition the management software is backward compatible, so it is possible (or likely) that users of older 8-bit controllers are using the newest version of the management software.
For bulk orders please contact us at info@basecamelectronics.com
Capabilities
Possibility to manage the system on different platforms
Desktop systems: Windows, macOS, Linux. The firmware of the controller is user upgradable (through the GUI).
Smartphones: Android and some control from 3rd party vendors for Apple's iOS product (iPhone and iPad).
GUI (Windows, macOS, Linux): SimpleBGCGUI240b8.zip (5Mb ) Upper limit for PID values was increased to 255 (2.55 for I) Upper limit for RC speed was increased to 255 and its effect was decreased 4x times to get finer step in adjustment. This video is showing How to setup and install the USB driver and SimpleBGC GUI software on MAC OSX. If you disconnect the gimbal from SimpleBGC GUI a.

Open Serial API
Open programming interface for development of external control modules — both for software configuration and control of the board and for communication with various electronic devices.
Automatic tuning of PID parameters
Automatic tuning of PID parameters allows you to quickly prepare the system for work either at the initial settings or at changed conditions.
Support of systems with various hardware configurations
Flexible customization of the sensor orientation.
Support for a wide range of motors of various configurations and sizes.
Support several configurations of motor orders, including configurations with the tilted motor axes.
Support for two IMU sensors and external IMU for maximum precision
The system works with either one or two IMU sensors. The use of two sensors improves stability and accuracy in
Optional connection of a
Support for wide range of absolute encoders
Installing encoder on each motor greately improves system performance and extends the range of applications
Different algorithms of follow mode
Flexible configuration of the follow mode for each axis. Automatic switching of horizon axis mode from lock to follow in case of persistent camera tilt.
Up to five user-configurable modes of system operation selectable with a toggle button
5 profiles grouped in 5 profile sets allows changing modes of operation or even hardware configurations
Support of a wide range of external control protocols
Futaba, Spektrum, 5x PWM, Sum-PPM, 3 ADC, Serial API
Flexible configuration allows for control of any functions of the system (every parameter that the system uses is configurable).
Battery voltage drop compensation
Battery voltage drop compensation ensures proper control of the drive motors during the whole life of the battery.
Different versions of the controllers for different needs
The licensing system allowed our partners to launch different versions of controllers for a wide range of applications: from compact controllers for stabilizers of light cameras to powerful ones for the stabilization of heavy units.
Ongoing work to improve the system
BaseCam Electronics is working closely with the developers of end devices, which allows us, on the basis of feedback, to continuously improve the stabilization algorithms and expand the capabilities of the system within a single version of the controller.
The principle of the camera stabilization using brushless direct drive motors
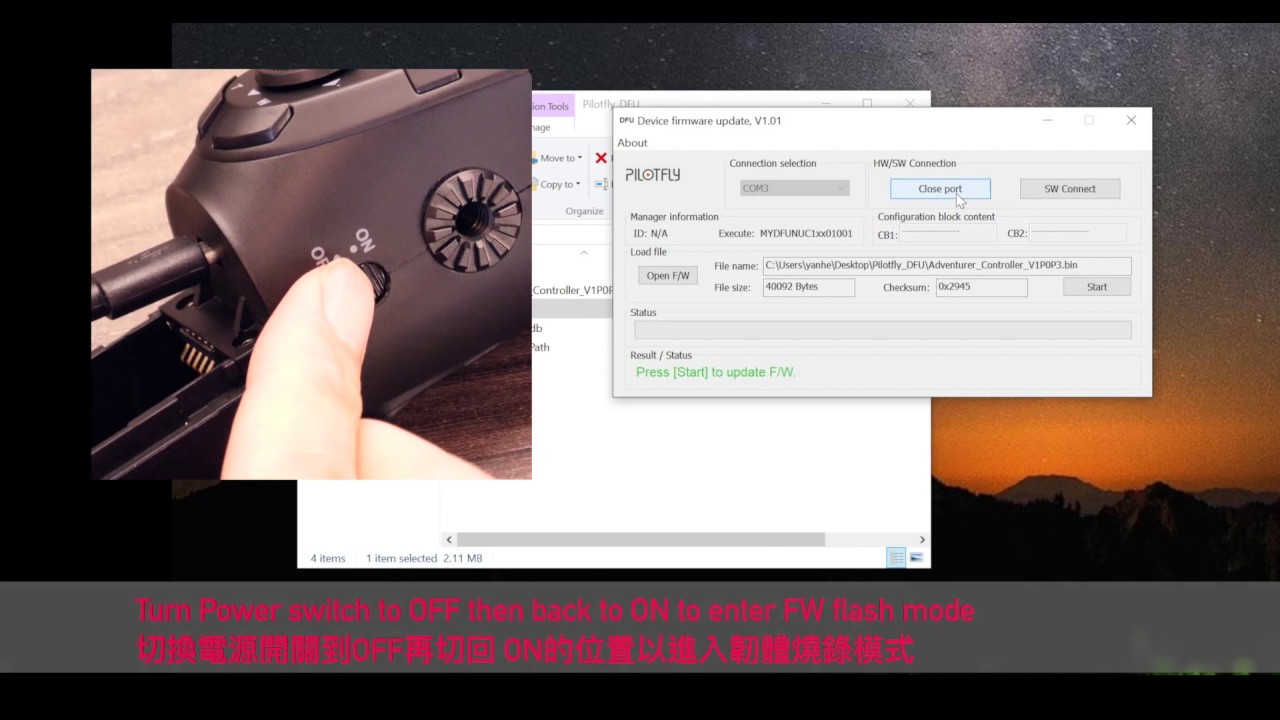
In fact, gimbal based on BLDC motors is very similar to regular gimbal based on hobby servo. The main difference - each axis of rotation passes through the center of gravity (CG) of the 'Camera + frame' system and rigidly connected to the BLDC motor. The absence of gear - a fundamental point that lets you use the inertia of the system is not to harm, but for good. In case of ideal balance of the camera, the rotor rotates freely without resistance and even without need of applying extra control force, which allows the camera to unleash from the disturbance from UAV frame. In addition, there is no backlash inherent gears or belts.
To control the motors, a special controller was designed. It receives information from gyroscopes and accelerometers mounted on the camera platform. A standard IMU algorithm is used to define camera inclination angles. With the remote control, operator sets desired tilt angle. PID-controller calculates the amount of compensation and send command to the power unit, which controls the current in the windings and thus the direction of the vector of magnetic field in the stator. Magnetic field moves the rotor to the right position.
Due to using IMU, mechanical part of the system is a very simple. There is no need in complex and expensive high-definition encoders for each axis. Just mount tiny IMU board on the camera platform, connect wires to controller and motors and all done!
It gives impressive quality of stabilization compared with regular servos.
Simplebgc Gui For Mac Windows 10
Basic requirements for the mechanical design of gimbal frame
- The possibility of precise balancing on three axes. The better the balance, the lower the current need for stabilization.
- Mechanical rigidity of bearing elements to prevent resonances from working propellers in flight.
- Minimizing friction in the joints. The better the gimbal axis are unleashed from UAV camera platform, the less effort is required from the engine to stabilize
- Elimination of vibrations from the main UAV frame. The vibrations have a negative impact on the quality of the video. But another negative effect in this system is that vibration will lead to self-excitation of the closed-loop controller.
Dimensions, mm
Rev. B Features
- Protection FET handles more current
- Better current distribution
Rev. A Important Notes
A. Some versions of this board may have minor error in labeling outputs: On boards having the
B. Some versions of the controllers can have a problem with the spektrum port: satellite receiver does not get enough power from the 3.3V internal voltage regulator, and it may function incorrectly (simptoms: signal interrupts, LED blinks randomly, on binding attempt system goes to reset). Possible workarounds:
1. Power the receiver from an external 3.3v power source (preferably a regulated battery supply).
2. To solder additional 3.3v LDO regulator into the controller. The best choice is 3-lead TO-92 package (for example, LP2950-33, L4931CZ33-AP, L78L33-ACZ). Soldering additional LDO voltage regulator 3.3v
Specifications
Rev. A | Rev. B | |
---|---|---|
Size of the board | 50×50 mm | 50×50 mm |
Distance between the mounting holes | 45 mm | 45 mm |
Diameter of the mounting holes | 3 mm | 3 mm |
Power supply voltage | 8–25 V (3s-5s LiPo) | 8–26 V (3s-6s LiPo) |
Maximum motor current | 1,5 A* | 1,5 A* |
5V output current to power external devices | up to 1 A | up to 1 A |
3V output current | — | 50 mA |
* Maximum motor current 1,5 A — total current for three motors.
For example, one motor can take 1 A, two other 250 mA each — but the total current should be no more than 1.5A.
Downloads For 32-bit Boards : BaseCam Electronics
Downloads
USB Drivers for PC Connection
If controller being connected to the USB port, is not recognized as COM-port, most probably you need to install or update drivers for CP210x chip. You can download driver for your OS from the manufacturer of CP210x.
AN IMPORTANT NOTE: The latest version (6.7.4) of driver for Windows may cause problems with delay in data transmission, visible as a big lag of the GUI. In this case, install version 6.7.2 of the driver, which had no such problems. Download version 6.7.2 driver.
Support
Type your question or comment below. Answer will be sent at your e-mail within 24 hours on workdays.
Great news the most up to date version of the Beholder EC1 3-axis camera stabilizer is arriving next week. Take advantage of our pre order discount of $50 off.
How Setup Simple BGC with Windows or Mac OS for Beholder EC1.
1. Download the Simple BGC GUI from Downloads for 32-bit boards.
2. Download Silabs USB to UART driver, choose the correct driver for your OS.
3. For Windows users launch the .EXE file. For Mac OS users go to step 4.
4. For Mac OS users download Java, once installed launch Simple BGC from the .JAR file.
Always read each program's installation notes for further technical assistance with connection and installation. Also to turn on the EC1 to allow Simple BGC to detect the stabilizer from the mini usb port.
Simplebgc Gui For Mac 10.10
Enjoy, Guru.
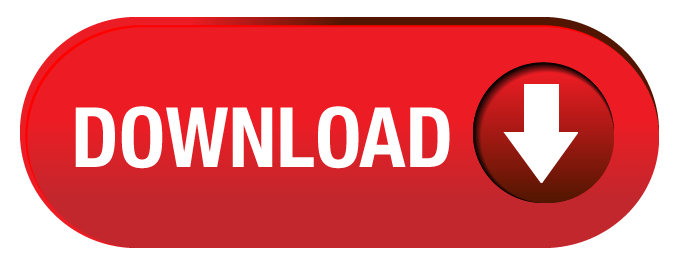